New turbine technologies offer unprecedented flexibility.
Scott M. Gawlicki is Fortnightly’s contributing editor based in Hartford, Ct. Email him at: sgawlicki@yahoo.com.
If there’s an electric power project under development that best reflects the current state of the U.S. gas turbine market, it might be the Northern California Power Agency’s (NCPA) 280-MW, natural gas-fired combined-cycle plant in Lodi, Calif.
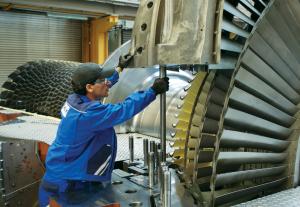
Scheduled for startup in 2012, the plant will serve some 14 different entities, including eight area municipalities. More important, it’s the first application of a new combined-cycle plant specifically designed to operate at a wide range of loads at 57-percent-plus efficiency and deliver up to 200 MW of power to the grid in just 30 minutes.
In addition to reducing the carbon footprint of the NCPA’s membership, the system—which the manufacturer, Siemens Energy, calls the Flex Plant 30 power island—will allow the agency to react quickly to the uncertain market conditions many expect will result when state-mandated renewable energy plants begin pouring power into California’s wholesale electricity pool.
In other words, the plant will provide financial cover, a hedge if you will, against whatever California’s energy future brings.