IT systems ease the pain of power plant restarts.
Scott M. Gawlicki is Fortnightly’s contributing editor based in Hartford, Conn.
Ensuring that power plant outages go smoothly has always been critical to the financial health of any power plant or electric utility. But in light of the current business environment, the financial stakes have never been higher.
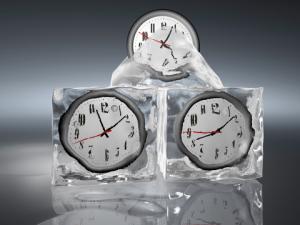
The reasons are many. New environmental regulations are forcing utilities—many with generating assets in different parts of the country—to decide whether to retrofit aging coal-fired plants or simply retire them. At the same time, low natural gas prices have utilities running more gas turbine plants for baseload duty.
Keeping nuclear refueling outages on-track has become more urgent as well, because sustained outages can lead to supply shortages and even blackouts. This is best illustrated by the current electric power supply concerns in Southern California due to the outage at Southern California Edison’s San Onofre Nuclear Generating Station (SONGS).
In any case, the close working relationship utilities have always had with their outage services vendors has become, by sheer necessity, even closer.
“Outage planning has become anything but routine,” says Charles Athanasia, vice president of thermal services at Alstom. “There’s incredible economic pressure on power generation facilities. In general, demand for electricity is down, environmental regulations are in a state of flux, and natural gas prices are low.”