Could local generators be used either to regulate voltage or control the power factor on distribution systems in New York?
John Kueck is a senior engineer with Oak Ridge National Laboratory and Darrell Massie is director, Mechanical Engineering Research Center, with USMA. Contact Kueck at kueckjd@ornl.gov.
Reactive power is becoming a hot issue in many regions of the country. Regulators and grid operators are grappling with ways to account fairly for reactive power supplies, and to encourage such resources to come online where they are needed. These analyses, however, are largely ignoring a vast fleet of infrastructure already installed on the network—namely, on-site generators and motors.
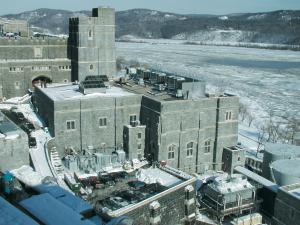
West Point military academy, for example, has four small synchronous generators that are used for combined heat and power or emergency power applications. If these generators also were used as synchronous condensers, they might supply additional revenue to pay for the distributed energy investment.
These engine generators already have been purchased, so the only costs in supplying reactive power would be the internal losses and some nominal equipment expenses.
Other options to control power factor is use of microturbines or adjustable speed drives. The payback on such solutions can be quite attractive, and merit a closer look as policy-makers consider how to account for reactive power.