Urbint
Lindsay Jenkins is VP for strategy and technical operations at Urbint.
How often do we meet someone for the first time and come away thinking, whoa, that guy (of either gender) is a genius? Well, that's what happened when we got to talk with Dr. Lindsay Jenkins, a Vanderbilt Ph.D. in civil engineering, no less, who as you can see in our discussion recounted below, has applied her smarts to safety.
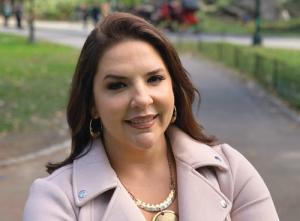
Specifically, protecting the safety of the workforce, which is no coincidence because her dad's career was in utility field work. Dr. Jenkins and her team at Urbint use artificial intelligence to assess the risk of unsafe outcomes in extraordinary detail, but there's nothing artificial about how they come at this very important task.
PUF's Steve Mitnick: What's your typical day like as VP of Strategy and Technical Operations at Urbint?
Lindsay Jenkins: I'm a bit of a bridge between our corporate strategy and where we're going from a product perspective, as well as engaging with our clients and supporting implementations and understanding our client needs.
I also work with our machine learning team on model support. On a typical day I might be meeting with a client and checking in with them on the effectiveness of their programs.
I might be soliciting some input from a client on a new product or a new feature that I'm working on. Then I could be working with our product engineering and customer success teams on work that's done behind the curtain to build a product that delights our customers.
PUF: What special training or degrees does your staff have?
Lindsay Jenkins: We have an entire team dedicated to machine learning, and that team is supported by data scientists, as well as talented engineers who are able to take our customers' problems and their data, curate it, and supplement it with existing data from Urbint's Model of the World to develop solutions to these problems. They also translate those solutions into something operational and usable in our applications.
That's what I like to call the last mile of delivery for our model.
Something that I do in my role is connect that back to operations, with a utility operations background and understanding and garnering an empathy for the workflow of our end users. We work with our customers to show them how to put these models and tools to use to see the ROI and effectiveness of a program, be it from reducing third party damages, given the number of damage prevention specialists they can deploy, or being able to reduce emergency response times, or increase the amount of safety observations.
PUF: What's the idea of the term Urbint Lens?
Lindsay Jenkins: We call it Lens because at the root of everything we do, we're essentially providing that lens or view of operations on a day to day or week to week basis. We're providing decision support in near real time.
All our solutions are based upon our field risk mitigation platform, which is built to identify the risk to workers as well as the assets they maintain.
Our new solution, Urbint Lens for Worker Safety, follows this model.
PUF: How are you improving safety?
Lindsay Jenkins: Worker safety is an issue that all our customers face right now. Urbint Lens for Worker Safety is a natural extension of the approach we take to damage prevention.
Urbint Lens for Damage Prevention assesses the risk of excavation activity on a localized level. The 811 ticket comes in and you're able to assess that risk of the excavator hitting a line.
We're expanding that way of thinking out more broadly to consider not only excavation, but also pipeline construction and constructing electric assets and assessing the risks to the workers who are performing that work on a daily basis.
We all have a story, if you've been in construction long enough, of unfortunately, a workplace injury or hazard. This challenge is personal to us, as it is to our customers.
Serious incidents and fatalities are not going down. The slight incident rate, which includes things like minor slips, trips, and falls, is going down in the construction industry, but not the rate of serious incidents and fatalities. It's a problem that needs to be addressed, and Urbint feels like AI can help solve this.
PUF: How can AI help?
Lindsay Jenkins: Research has shown that workers can only identify forty-five percent of work site hazards on their own, even if they've been in the industry for several years. It's just a reality of our cognitive abilities as humans. We can't see some of these things. But missing more than half of threats is like doing work with one eye closed.
There are some leading indicators that can be used to identify additional hazards on a job site, given the planned work for that day. That's where AI can help solve this problem.
If we know the work that's being done, the site conditions, and the conditions of the crew performing that work, we're able to provide decision support to identify that this is the riskiest task, as well as the riskiest project you have in your portfolio. So, we can say, here's where you need to perform an intervention or put in an engineering control to help bring down that overall risk.
PUF: That safety hazard rate of recognition must be much smaller for new workers, but they need it.
Lindsay Jenkins: Yes, we have newer workers who are on these job sites with less experience and less exposure to some of these hazards. They don't have the benefit of learning on the job. This is where our worker safety solutions supplement that as we are connecting and leveraging the utility's own data from their incident and safety management systems.
We're able to apply those learnings that, on a project three years ago, we saw a tendency for this unsafe outcome. We can apply that learning directly to the job that's being performed that day, instead of overwhelming supervisors with, here's what happened last week on multiple projects, which may not be relevant to what they're working on today. Through AI, we're able to connect those learnings in real time so they can supplement that experience gap of newer supervisors and personnel.
Sometimes on the flip side, we have folks who have been on the job for forty plus years and they get a little complacent. Maybe they decide they don't want to take the proper safety equipment with them. By having this tool, forcing that dialogue and review, we help make sure folks with fifty years of experience are as properly protected as folks with no experience.
PUF: How does this work?
Lindsay Jenkins: Our tool is built to be deployed on mobile devices that our partners use in the field, like an iPad or Toughbook. Logging in for the day, you would be able to see the specific risks and a risk score for the task you're performing.
Say you're constructing a pipeline that day, and there's a lot of activity going on. You could be stringing the pipe or moving that material, which is dangerous, or you could be trenching.
Those unique tasks like trenching, welding, and pressure testing, are all identified in their application and they're color coded by risk. The risk is associated not just taking into account the task that's being performed, but also site conditions where you're doing that task.
If I'm trenching in my backyard right now in Fort Worth, where it's nice and warm and there's not a lot of activity around me, I'm going to be okay. If I'm doing that same activity in the middle of a snowstorm in Midtown Manhattan, that elevates the risk.
We are also beginning to assess the leading indicators, or a safety culture score for projects. We evaluate, for the people working on this project, what has been that contractor's safety history and is the crew being overworked?
Are they tired or feeling rushed because the project schedule is behind? Have we seen them perform well on other site-related audits? Then we start to understand what the condition of the people doing the work on that project is. Those three variables, task risk, site conditions, and safety culture are all combined in an overall risk score you can use to decide whether or not to add a targeted intervention.
To take this full circle, let's say you were performing a hot tap of a transmission pipeline and that showed up as the highest risk item. The intervention may be �" because of certain safety culture issues, and the nature of the work �" that you have an engaged conversation with the contractor who's planned to do that work.
You make sure they can play back to you what the proper procedure is for doing that task, as well as what they would do if something went wrong. Then you make sure everyone's aligned.
We provide this decision support capability to enable the supervisors and safety personnel to focus on what is the riskiest and start to have that conversation. A lot of the results we see are the output of a dialogue with our damage prevention crews and excavators.
We're trying to help supervisors to know where they should be focusing and having those conversations with their contractors and personnel.
PUF: Does it have to be customized? If you're with Eversource in Boston versus down here, is it the same or does it get customized for their particular conditions?
Lindsay Jenkins: Yes. That's where our Model of the World is able to feed in the unique conditions that one might experience in Boston as opposed to being in Hot Springs, Arkansas, or Texas.
We're able to customize workflow so that if there's a certain way a utility approaches a job hazard analysis, or a site observation, we can enable that. The beauty of this solution is as we have more adopters and we're collecting more data on task and project risks, as well as interventions that have been pursued to help mitigate that risk, all of our customers will benefit from the learnings across the country.
Another beauty of machine learning and AI is that we keep on developing richer datasets that we can leverage to continuously improve our model.
PUF: Look out to the future three or four years. What will be the impact?
Lindsay Jenkins: I believe we'll have a significant and measurable impact on reducing serious incidents and fatalities.