Wireless systems are improving front-line processes.
Scott M. Gawlicki is a Fortnightly contributing editor based in West Hartford, Conn. Email him at s.gawlicki@excite.com.
If there’s a U.S. business segment that’s been slow to embrace today’s most advanced mobile workforce management technologies, it’s the electric power industry. That, however, has finally begun to change as electric utilities throughout the country are rolling out an assortment of mobile workforce solutions, many of which already are found in other industries.
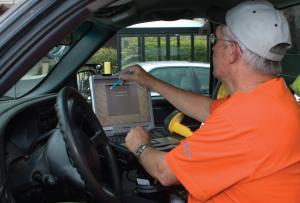
In addition to making it easier for employees to do their jobs, these solutions promise to improve operations, significantly reduce costs, and limit the occurrence and duration of forced outages.
Three mobile workforce solutions recently were implemented at National Grid in Long Island, New York, FirstEnergy in Akron, Ohio, and Idaho Power in Boise, Idaho. Each demonstrates the state of the art in a different slice of the operations pie: power generation, distribution system operations, and customer service.
National Grid
For employees at National Grid on Long Island, operational data is just a phone call away.
In 2006, KeySpan’s electric generation division (acquired by UK-based National Grid in 2007) introduced a mobile workforce management pilot application from Transpara Corp. that provides real-time power-plant operations information to employees through a company-supplied cell phone.