Total cost of ownership accounting optimizes long-term costs.
Steven McCabe (stmccabe@deloitte.com) is senior manager with Deloitte. Kwasi Mitchell and Nathan Ives are managers with the firm.
A large regional utility forfeited significant operating revenues after it replaced pulverizers at several of its coal-fired power plants. Because the replacement pulverizers were sized to operate at 100-percent capacity during operations using the coal typically procured by the utility, upgraded plants had to be derated following a change to lower BTU-rated fuel.
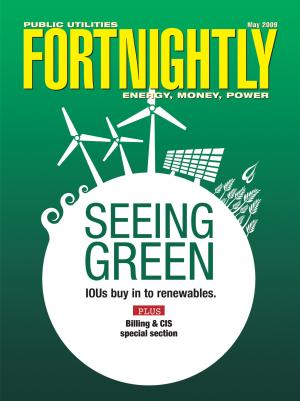
If utility decision makers had used a total cost of ownership (TCO) framework, they could have avoided this situation. An operations and maintenance cost assessment would have revealed the operational effect of the fuel change, allowing the company to consider oversized pulverizers to accommodate lower-grade fuels and thereby maintain the power plant’s capacity.