Capture and storage tech developments secure coal’s future.
William Atkinson is a Fortnightly contributor based in Carterville, Ill.
Carbon capture and storage or sequestration (CCS) involves isolating carbon dioxide (CO2) from other power plant emissions before it is emitted from the stack, compressing it into a liquid, and pumping it into underground geological formations such as spent oil or natural gas wells, saline reservoirs, or inaccessible coal seams.
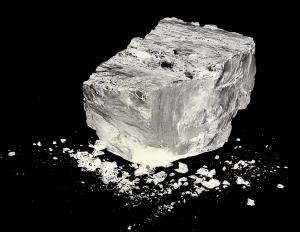
A 2007 study released by the Electric Power Research Institute (EPRI), found that U.S. electric utilities can help the nation cut its CO2 emissions to 1990 levels by 2030 by taking aggressive steps in seven areas. The most significant reductions, according to the study, would come from CCS technologies.
The National Energy Technology Laboratory (NETL), in its “NETL 2007 Carbon Sequestration Atlas,” reports that North America has enough storage capacity at its current production rate for more than 900 years of carbon dioxide.