Avoiding pitfalls, realizing benefits.
Nathan Ives (nives@deloitte.com) is nuclear utility service offering lead in the power and utilities practice at Deloitte Consulting LLP, and Steve McCabe (stmccabe@deloitte.com) is utility supply chain lead at the firm. Gary Gilmartin (ggilmartin@Gengineeringworks.com) is executive director of the Oak Ridge Energy Corridor and Tennessee Valley Nuclear Energy Coalition.
Increasing demand for clean, affordable, base load electricity, combined with rising public support for nuclear generation, presents utilities with the opportunity to build new nuclear plants for the first time in more than three decades. But unlike the birth of the nuclear generation industry, domestic suppliers of many critical nuclear plant components and skilled workers are scarce. And with some internationally sourced component delivery times increasing, the situation is getting worse. Subsequently, the risk of nuclear generation construction project delays will persist and might increase unless participating company supply chains can effectively reach across international borders.
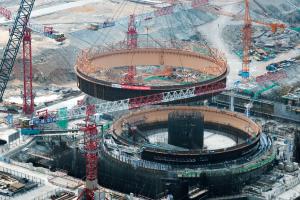
Power generators seeking to build new nuclear generation face a protracted construction timeline and an estimated $10 to $18 billion 1,2,3 up-front capital investment, making the economic attractiveness of nuclear generation largely dependent on the plant’s construction timeframe and capital financing structure. Therefore, factors slowing new nuclear plant construction significantly impact the overall financial viability of the project and demand preemptive executive action to prevent occurrence.