A strategy for completely removing mercury from environmental emissions.
J. Michael Burton is a Founding Partner with Natural Environmental Solutions (NES) and currently serves as CEO. Scott Hurst, Ph.D. is a physical chemist, a co-founder of NES, and an Associate Professor of Chemistry at West Virginia University Institute of Technology. Richard Squire, PhD is a Professor of Chemistry at West Virginia University Institute of Technology with more than 35 years of experience designing and starting-up a number of commercial facilities highly hazardous chemicals, without incident. Jay Wiedemann, PhD is an Associate Professor of Chemistry at West Virginia University Institute of Technology.
Mercury is a trace element in coal which currently is emitted from coal fired electric generating power plants. The ultimate presence of mercury in the environment results in a cumulative poisoning of people as illustrated in Figure 1.
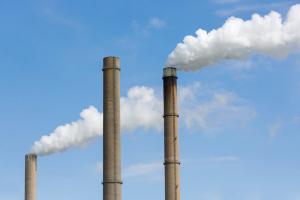
Many industries produce contaminants such as mercury as byproducts in their production processes which are expelled in the air and water as pollutants into our environment. These contaminants have been deemed detrimental to our ecosystems in general and human health specifically and are thus heavily regulated. Ironically, the EPA cites recent increases in the contamination of waterways as attributable to industry's increased use of clean air technology. Such is also going to be the case when powered activated carbon (PAC), a sorbent which can capture most of the gaseous mercury from coal-fired power plants, is used. As illustrated in Figure 2, mercury will then be spread throughout the power plant processes in an effort to clean the air and much of it will end up in the retention ponds. There, anaerobic bacteria has a high probability to transform the toxic mercury into the highly toxic methyl mercury.
What is needed is technology that removes the mercury and concentrates it in a single small location instead of contaminating our air and waterways. We have such a process, discussed below.
Since there seem to be no two power plants in the US which are configured the same, a common solution is desirable. An assumption built into our solution is that nitrous oxides (NOx) and sulfur oxide (SOx) are removed before the mercury treatment system. The mercury removal equipment will be installed prior to the final emission stack. There are two treatment options for mercury removal: one is chemical and the other is biological. Both require a catalytic oxidation of the exit flue gas stream followed by a high-efficiency, low-pressure-drop water-based scrubber.
Let's first consider a chemical treatment option. In this case, the function of the low-temperature oxidizing catalyst is to convert all mercury to the water-soluble oxidized mercury (charge +2), identified by the symbol Hg(+2). Next, a circulating water-based scrubber will capture the Hg(+2) and pump a draw-off stream to a proprietary concentration and treatment facility to remove and concentrate the mercury (Figure 3). Mercury Hg(+2) is reacted with sodium sulfide, precipitated, filtered, and removed as a small amount of solid waste. Several methods of treatment are available.
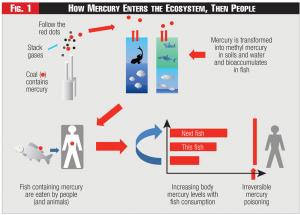
Now let's consider a biological treatment option. While more cumbersome to operate than a chemical treatment, bacterial treatment has some superior features. The crucial component of the mercury bacterial removal process (Figure 4) is a very special bacteria complex.
Since mercury is harmful to most living organisms including bacteria, how does this bacterium survive? It contains a group of genes that when activated by the presence of any form of mercury, say Hg(+2), initiates the task of tightly capturing the water-soluble Hg (+2) entering the cell, transferring it to another protein which reduces it by adding two electrons, and then frees the water insoluble Hg (0) which diffuses out of the cell. Since this is a water environment and mercury is heavy, it drops to the bottom of the system. The water is then free of mercury. A parallel process in these bacteria will remove organomercury compounds such as methyl mercury and the result is also elemental Hg (0). The bacteria can be sensitized to convert much larger concentrations of mercury (up to 100 ppm) than the native species.
The cost of equipment for removing and treating mercury from the flue gas is estimated for a 3GW facility, roughly the size of the John Amos generating plant. The scrubber used for capture of mercury from the flue gas needs to be efficient and have a low pressure drop. Then, since Hg(+2) is soluble in water (over 3% ), all of the mercury can be captured and processed either chemically or bacterially. A number of other flue gas metals can also be removed (Figure 3).
Similar mercury bacteria reduction equipment configurations can be used on both coal and fly ash impoundment ponds with the capital costs per gallon decreasing significantly both with larger facilities and more concentrated mercury. As indicated, the figures in parenthesis are ideal cost projections. The catalyst and scrubber were estimated since we have not been able to obtain a flow chart from an operational facility. There could, of course, be additional costs, for example, to maintain plant operation during tie-ins. The concentration and treatment are based on completed estimates from other projects for concentrating and treating 5 million gallons of water per day, see Figure 5. The total is $40 to 60M +/- 30%; add 30% additional based on "unknown field conditions," say 70 to 90$M. For this amount a 3GW site can eliminate mercury air and water emissions. Further, the impoundment ponds can be lowered by using the excess treatment capacity without concern of releasing the highly toxic methyl mercury into the waterways as mentioned earlier.
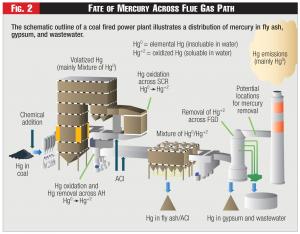
It is important also to consider overall strategy in light of implications of the Mercury and Air Toxics Standards (MATS) promulgated by the U.S. Environmental Protection Agency (EPA).
Based on the MATS table for emission limits, a 3GW facility will generate about 6 pounds of mercury per day, which can be completely captured by either process.
The chemical unit operations used here are well understood and are also successfully operated in a number of industries in a fully automated mode. Further, the design basis is well established and the operation proposed here is well with these limits. There are a number of companies that offer a turn-key instalation, and others that add full operation of these facilities. Specifically designing equipment to capture mercury allows the remainder of the upstream equipment to operate as it was designed instead of compromising its integrity by retrofitting it for PAC and corrosive oxidant addition. The mercury equipment can be quickly taken off-line with no implication for the operation of the generating plant.
Based on thirty years experience in the chemical industry, we believe that PAC and other previously proposed solutions to reduce mercury emissions will be a marginal operation at best; in and out of compliance with large amounts of residue pumped to the impoundment ponds. Very large impoundment ponds will be needed to contain the higher concentration of mercury and the highly hazardous methyl mercury, so they must be lined with expensive materials and treated with chemicals to prevent mercury seepage. Containment of this nature cannot be indefinite and a leak or overflow would become a major event since there will be methyl mercury present. The cost will exceed the estimate above and still not be a permanent solution.
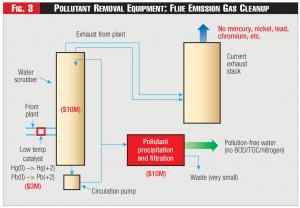
Creating even larger storage ponds for mercury-containing wastes is another step in the direction of sacrificing the quality of our waterways for air quality. The trend needs to stop by fixing the problem as opposed to moving it to a different location. By containing both more volume and higher concentration mercury-laden waste in ponds there will also be a potential to generate highly toxic methyl mercury. (See Figure 1.) These containment lakes will need considerable investment and will become enormous as there appears no technology other than the one suggested to satisfactorily remove mercury and methyl mercury. The South River and south fork of the Shenandoah River are a testament to the fact that there currently are no operational methods to detoxify the source of the methyl mercury or decontaminate the river; the biological process outlined in this note has not been tested for this use despite our best efforts. After testing numerous real samples for more than four years, the processes described here have no known limitations, thus qualifying as a legitimate alternative for all mercury removal and containment. Six pounds of mercury a day is roughly a ton of liquid mercury a year in a small tank or a solid waste in an appropriate waste dumpster, versus a concentration of 30 ppm mercury compounds in millions of gallons of contained water; our option allows solution of the problem in a cost-efficient complete manner.
Lead image © Can Stock Photo Inc. / kruwt