Technologies are scaling up quickly to meet industry needs.
Scott M. Gawlicki is Fortnightly’s contributing editor, based in Hartford, Conn. Email him at sgawlicki@yahoo.com.
Like other California electric utilities, San Francisco-based Pacific Gas & Electric (PG&E) has been scrambling to meet the state’s renewable portfolio standard (RPS), which requires suppliers to obtain at least 20 percent of their power from renewable energy sources by 2010.
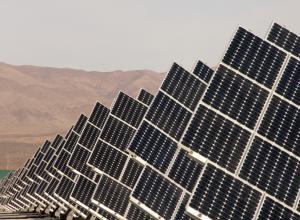
Though the RPS includes a variety of technologies, renewables developers are choosing utility-scale solar power more than any other resource, says Hal La Flash, PG&E’s director of emerging clean technologies.
“We solicit offers for renewable energy every year,” he says. “This year (the response) was 80 percent solar. Part of that is because the best wind and geothermal sites are already under contract. But solar, especially photovoltaic technology, lends itself to a modular approach and you can develop more projects on a smaller scale.”
Without question, solar power is hot these days. PG&E alone has contracted for more than 1,500 MW of photovoltaics (PV), including 250 MW it will own and operate, and nearly 3,800 MW of thermal solar power capacity. Other utilities, including Florida Power & Light and Southern California Edison (SCE), are following suit. And that, in turn, is driving R&D investments designed to improve solar plant output, reduce equipment costs, and challenge the argument that solar power will cause headaches for fine-tuned utility operations.