Continuous improvement requires changing practices and cultural norms.
Hossein Haeri, Ph.D., is an executive director, Heidi Ochsner an associate and Jim Stewart, Ph.D., a senior associate at The Cadmus Group, Inc.
Pending legislation, maturing energy-efficiency programs and lower avoided costs are severely limiting program administrators’ ability to acquire cost-effective efficiency resources to meet their portfolio goals. It’s time to look in new places for economic, long-term savings. Activity-based options in the industrial sector that revolve around continuous energy improvement would be a good starting point.
Where Have All the Savings Gone?
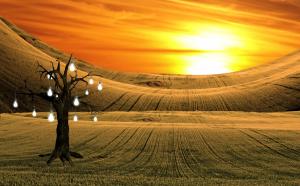
The Energy Independence and Security Act (EISA), signed into law on Dec. 19, 2007, is by many accounts the most sweeping energy-efficiency legislation ever enacted in the United States. Perhaps one of EISA’s most far-reaching provisions is the standard for efficient light bulbs under Subtitle B—Lighting Energy Efficiency, Section 321. The provision directs the Department of Energy to set performance standards for general service light bulbs with 25 to 30 percent savings compared to traditional incandescent bulbs, beginning in 2012. Once fully implemented, the act will essentially eliminate conventional 40-watt, 60-watt, 75-watt, and 100-watt screw-base incandescent light bulbs by 2020. The act sets equally dramatic energy-efficiency standards for weatherization and energy-using equipment and appliances.