Waste fuels struggle despite coal’s decline.
William Atkinson is a Fortnightly contributor based in Carterville, Ill.
Shale gas has changed the game for power generation fuels in America. With gas prices projected to remain low for years or even decades to come, coal-fired power generation in particular faces a dim outlook. Most new coal projects have already been sidelined, and now, cost pressures and changing environmental policies are forcing utilities to re-evaluate their plans for existing coal plants—especially those that are nearing the end of their useful lives.
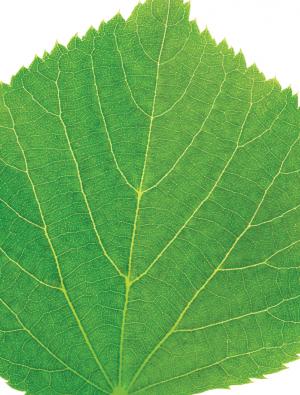
Many such plants are being mothballed or decommissioned. In late 2009, for example, Exelon announced it would permanently shut down four Pennsylvania coal-fired generation plants with a total capacity of 933 MW. Around the same time, Progress Energy announced the closure of 11 North Carolina coal-fired plants with a total of 1,500 MW. And in mid-2010, TVA said it would idle nine coal-fired power units, with the goal of replacing them with low carbon or carbon-free generation.
Natural gas seems destined to become King Coal’s successor, and the dash to gas is causing resource planners to consider ways to ensure ongoing fuel diversity. Solar and wind have a role to play in the country’s generation future, and energy policy trends favor some level of nuclear power expansion. However, often lost in the shuffle is another fuel—one that doesn’t have the glamor and glitz of solar, wind, and nuclear. This fuel is biomass.