MATS compliance now, with flexibility for the future.
Kevin Crapsey is vice president of corporate strategy and development at Eco Power Solutions.
Many in the power generation industry are still scratching their heads one year into the glide path for compliance with the Mercury and Air Toxics Standards (MATS) issued in February 2012. With only two (or three) years remaining, most utility executives are still trying to figure out how to comply, rather than deploying solutions. Whether they view MATS as a target on the industry’s back or an opportunity to save the environment for future generations, it’s an industry reality. So how does the industry balance this reality with its responsibility to serve consumers and earn a profit for investors?
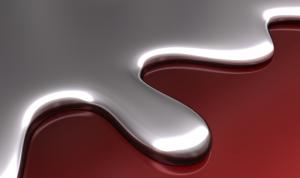
Emission control technologies have been helping the power generation industry reduce its pollution output since the Clean Air Act of 1990. The myriad methods and technologies applied to date have significantly reduced plant emissions, with a 27 percent decrease in particulate matter (PM) 2.5 between 2000 and 2010, according to the U.S. Environmental Protection Agency (EPA). However, MATS puts power plants on a strict three-year timeline to reduce emissions of heavy metals (including mercury, arsenic, chromium, and nickel) and acid gases; and EPA updates to the Maximum Achievable Control Technology (MACT) rules require power plants to periodically revisit their control strategies.
This compliance burden falls primarily on a handful of industries and their customers. Among those affected are the many energy producers and industrial producers of cement, steel, and aluminum that rely on the aging coal-based technology responsible for about 80 percent of total U.S. emissions of sulfur oxides (SOx) and nitrogen oxides (NOx). The MATS ruling will force these industries to identify and implement alternatives in a very short timeframe, while facing the ongoing challenge of remaining competitive in the face of current and and future requirements for emissions reductions.
Targeting Mercury
While many options for removing mercury are commercially available, technical challenges remain that could create delays in meeting the MATS deadline. Different types of coal release different amounts of mercury. Mercury capture in electric generating units that burn medium- or high-sulfur coal remains prohibitively expense in some cases.
During August’s MEGA Symposium in Baltimore, several presenters attempted to tackle the best ways to remove mercury to meet MATS. While most of the strategies presented work, two significant issues remain: consistency in mercury removal and mercury re-emission at the stack. These two issues, more than anything, are causing delays for power generators to meet the MATS deadline for compliance.
The oxidation of mercury is very site-specific. So much so that two locations that are exactly the same and burning the same coal will have very different mercury oxidation levels. This, then, requires each plant’s existing technologies be managed in ways unique to that facility. This lack of consistency in execution will be an ongoing issue for utilities and, in the end, could drive up costs. Addressing mercury re-emission at the stack is an even bigger challenge. Currently, there’s no proven commercial solution to the problem.
As a result, utilities will continue to struggle with consistently oxidizing mercury and removing enough of it to further minimize re-emission. At the end of the day, mercury re-emission remains a huge problem for the industry.
Electric utilities have expressed a great deal of concern about their ability to comply with MATS within the given timeframe. They also must consider that a growing number of emissions are being targeted for regulation as part of a more holistic regulatory approach.
Shut Down or Switch Fuels?
Throughout the power generation industry, companies are weighing the costs and benefits of several different solutions for meeting the emission reduction standards. At first, this can be daunting because emissions control on this scale has never been done before. Due diligence requires close examination of new and existing emissions control technologies to ensure that they comply with regulations while meeting power generation needs.
This uncertainty has led some electricity generators to simply shut down the emitting facilities altogether. While this addresses the emissions reduction problem, it has tremendous grid reliability implications and can affect the reliability of electricity delivery to customers, particularly in remote areas. And likewise, these mostly older assets are profit centers that have already been written off the books.
Another option is to switch to a different, cleaner fuel source—typically natural gas—and shoulder the large expense of a fuel-change retrofit. However, there are no assurances that the price of natural gas will remain low. These prices have traditionally fluctuated and environmental concerns about hydraulic fracturing could put an end to that practice and low natural gas prices.
Conflicting Demands
While these options will reduce emissions, it’s important to understand their context amidst the nation’s energy demands. According to 2008 figures from the Edison Electric Institute, the association for shareholder-owned electric companies, approximately 800 U.S. coal-fired power plants—or about 65 percent of current U.S. capacity—are between 31 and 60 years old. Retiring all of this capacity or replacing a percentage of it with cleaner fuels aren’t viable options for power companies with an obligation to serve their customers and remain economically competitive for their investors.
These realities mean that coal-fired power generators need to look to emissions control technologies to continue operating their facilities, but with fewer emissions. A variety of different emission reduction technologies can target mercury emissions and comply with MATS. While they cost less than building a new plant or switching fuels at an existing plant, the price tag can be hefty. Another constraint to this approach is the space required for its equipment, especially at older facilities that are typically already tightly packed into a limited land area.
Numerous proven options are available to reduce emissions. Flue-gas desulfurization (FGD) targets SOx emissions, but what about NOx? Selective catalytic reduction (SCR) technology can handle NOx emissions, but what about PM emissions? That’s when an electrostatic precipitator comes into play. But then, what about MATS? Can existing mercury control technologies provide consistent removal rates or address mercury re-emissions at the stack?
Electric utilities and industrial facilities are facing the reality that mercury emissions control is part of a larger multi-pollutant emissions control approach that dates back to 1995 when EPA promulgated the Clean Air Interstate Rule (CAIR), Clean Air Mercury Rule (CAMR), and Clean Air Visibility Rule (CAVR). As has been noted, this marked a shift from an approach that addressed a single issue at a time to a more holistic approach (see “A Multi-Pollutant Strategy,” Public Utilities Fortnightly, January 2009).
But that’s only half of the equation. To achieve the goals of multi-pollutant emissions control, electric utilities and industrial facilities need the technology that allows them to meet the regulations. Until now, EPA’s holistic approach to regulating a broad range of emissions has run far ahead of industry efforts to perfect any one single-issue technology.
It’s a complex situation in need of a simple answer.
The need for a single solution has been driving engineers since the early 1990s. What they’ve come up with is a single technology that can reduce many different types of emissions and can be installed consistently across generating facilities.
Multiple Emissions, One Solution
Multi-pollutant emissions control systems hold the promise to overcome several of the drawbacks of traditional emissions control systems. This option, now being offered by several companies, uses a single system that removes multiple targeted pollutants from flue gas before they are released into the atmosphere. Through extensive testing, this form of emissions control system has shown that it can capture mercury, PM, CO2, NOx, SOx, halogens and other heavy metals.
Multi-pollutant emissions control systems offer extensive benefits to electric utilities searching for an option to meet rapidly approaching deadlines at a less disruptive cost. These systems regularly require a lower capital investment than a series of its traditional counterparts that would be needed to eliminate the same number of pollutants. This all-in-one approach allows utilities to meet current regulations while serving as a hedge against future regulations. It also allows systems to be installed more quickly and with a smaller footprint. Additionally, some of these systems use a modular design that ensures scalability for larger boilers and offers the potential for removal of CO2, providing an additional hedge against a potential cap-and-trade scheme or carbon tax.
The EPA has already stepped in and shortlisted several multi-pollutant control systems as part of its preliminary MATS ruling. The ruling noted that these systems “offer the potential of reduced compliance costs and improved overall environmental performance.” After extensive tests and demonstrations, many of these systems have proven to consistently reduce almost all mercury emissions and re-emissions, NOx, SOx, arsenic, chromium, nickel and other heavy metals and acid gases. Add onto that their tendency to be cheaper, easier to assemble on-site, and ability to be calibrated for future regulations on CO2, and you have coal’s domestic future in a nutshell.
There are a variety of companies that offer this all-in-one technology, but use different processes to achieve their emissions reduction goals. Proprietary ozone injection procedures, reacting the pollutants with the specialized catalysts and intricate introductions of organic material can, in fact, differentiate the emissions capture capability of one system from coal plant to coal plant. Each company’s system has its strong suit based on the size, location, and budget of a potential plant retrofit. Beyond the competition among these different vendors, multi-pollution control represents overall progress toward a more sustainable future. It shows that coal, without the hang-ups of environmental and health concerns, can still be a valuable resource in the 21st century.
The Price Tag
Multi-pollutant emissions control technologies have their own drawbacks. While less expensive than a series of traditional emissions control technologies or fuel retrofits, they can still carry a significant price tag. And, the current low price of natural gas remains the dominant factor in decisions about coal-fired facilities. Finally, some of these technologies have yet to been proven through demonstration projects or third-party testing.
However, the Electric Power Research Institute’s integrated environmental controls program (Program 75) is taking a leading role in providing independent engineering evaluations and performance and costs assessments for multi-pollutant emissions control technologies.
In one comparative study of a 500-MW coal-fired unit that compared a leading multi-pollutant emissions control technology to a traditional air quality control system (AQCS), EPRI found that the “technology has the ability to accomplish multi-pollutant (SO2, SO3, NOx, Hg, halogens and residual particulate matter) removal at very high efficiencies in a single absorber vessel.” In assessing the cost of this system, EPRI found that it “has a lower capital cost and fixed operating costs than the combination of traditional air quality control systems that would be required to achieve similar performance.”
This study demonstrated that the proven technologies that are available offer a strong alternative to electric utilities that must continue to meet the demands of customers, the EPA, and investors in the short and long term.
New Lease for Coal
Coal accounted for 42 percent of electricity generated in the United States in 2011. Therefore, it would seem nearly impossible to move to a portfolio that doesn’t retain a strong coal presence for the foreseeable future. A large-scale shutdown of coal facilities would have dramatic grid reliability consequences. And retrofitting to natural gas is both expensive and based on a hedge that gas prices will remain at this low level. These options likely will be used on a selective basis and most likely for economic reasons rather than to address environmental regulations.
Power generators will rely upon installing emission control technologies. This solution uses existing generating assets to address the need to reliably deliver electricity, and it addresses some existing regulations and possibly some future regulations. But relying on a patchwork of single-issue solutions to address this holistic challenge is an inconsistent approach with costs that quickly add up.
Taking a consistent approach that addresses current and future regulations with certainty is the most logical approach. Therefore, the question becomes not whether the industry will adopt multi-pollutant emissions control technology, but rather which utilities will be the leaders and when will they adopt this approach.