New technologies are helping windpower mature as a viable power supply choice for utilities.
Michael T. Burr is Public Utilities Fortnightly’s editor-at-large. E-mail him at burr@pur.com.
Few people understand how to ride shifting winds better than Jim Dehlsen does.
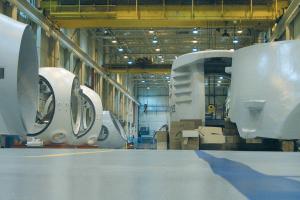
Dehlsen founded Zond Energy Systems 25 years ago, and steered the company through a series of major changes and challenges—the oil-price collapse of the 1980s; ambivalent energy policies, with on-again, off-again production tax credits; and the sale of controlling interests in Zond to Enron in the late 1990s.
Should it come as any surprise, then, that Dehlsen still is bullish on windpower’s prospects?
“The market is finally coming alive for wind,” says Dehlsen, CEO of Clipper Windpower, a highly Zondesque upstart that he co-founded with his son in 2001. “We’ve been at it for a long time. But only in the last couple of years have we seen a real willingness to make wind part of the mainstream power supply. And a lot of it is coming from utilities.”
Some of the reasons are simple. For starters, market economics have made windpower more attractive than it once was. While prices for fossil fuels have oscillated wildly, wind’s operating costs have held relatively steady. As a result, windpower has emerged as a nice, environmentally benign hedge against fuel-price risks, even if it isn’t a big percentage of total generation.